Case Study: Air Compressor Noise Control
Air Compressors installed in a corner of a light Industrial Facility with impact on assembly workers.
Abstract
Two air compressors installed at a light industrial facility near an assembly area used to run air powered tools in the manufacturer’s process. The compressors were mounted in the corner of the warehouse near two adjacent concrete walls. Management received numerous worker complaints about the noise emanating from the compressors and retained eNoise Control to provide noise mitigation recommendations. It was determined that, to meet the customers goal, the overall noise levels should be decreased by 10 to 13 dBA at 3 feet from the compressors.
Mitigation recommendations included:
- attenuate radiated compressor noise by erecting a sound curtain barrier wall,
- control reflected noise from the ceiling by adding a roof to the sound curtain wall,
- reduce reflected noise by adding acoustical absorption to the adjacent concrete wall and ceiling surfaces,
- construct a dedicated room to enclose the two compressors from concrete block or stud and gypsum board, and
- relocate nearby employees to a location further away from the compressors.
The client elected to implement recommendations incrementally. After the implementation of recommendations b and c the noise complaints ceased. Sound level validations were made. eNoise Control found that a 13 dBA reduction had been attained.
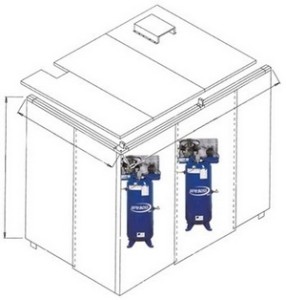
Air Compressor Noise Enclosure
The attenuation design, sound level measurements, and the effectiveness of the mitigation will be discussed.
Introduction
A growing light industrial manufacturer added a second air compressor when there assembly areas need grew. The new air compressor was located out of the way of facility traffic in the corner next to the existing air compressor. The air compressors were the vertical tank type with a 5 horsepower electric motor mounted on top of the tank. The assembly area was approximately 30 feet away from the location of the air compressors. Management received numerous complaints from employees in the assembly area after installing the second air compressor. Although the noise levels in the assembly area did not exceed OSHA guidelines, management was concerned with worker moral and reductions in productivity. This case study report accounts the experience. eNoise Control analyzed the noise sources, and provided environmental noise control recommendations. Our Acoustical Consultant made several recommendations to the manufacturer to mitigate the noise, some of which were implemented. The manufacturer decided to implement the recommendations incrementally. After two recommendations were implemented the complaints ceased, and eNoise Control returned to the site to conduct validation measurements.
Criteria
The manufacturer’s first concern was to lower the overall noise of the compressors and provide a safe working environment for their employees. The manufacturers other concerns were; (1.) ensuring the noise mitigation items would not impede the proper functioning of the equipment, (2.) ease of accessibility to the equipment for maintenance and repair, (3.) that the noise mitigation solution be movable and re-usable, if at a future date, they move the equipment, (4) overall cost of noise control solution. The design criterion was to decrease the noise levels by 10 dBA at 3 feet.
Procedure
eNoise Control viewed the air compressors and their layout in relation to the adjacent walls, ceiling structure and the assembly area. The air compressors cycled on and off due to the variable demands of the air tools in the assembly area. When work was idle each compressor would run for a few seconds independently to recharge its tank. This would occur at irregular intervals. When production was at full speed, both compressors would run simultaneously to keep up with the air demands. eNoise Control conducted sound level measurements at both of the described conditions. Measurements were made with a Casella 1/3 octave integrated spectrum analyzer, with an ANSI Type 1 precision 1/2″ microphone and preamplifier. Measurement results were analyzed and compared to the criteria. eNoise Control determined the amount of noise attenuation required to meet criteria, and developed recommendations to provide the prescribed amount of mitigation to the air compressors. eNoise Control returned to the site to conduct observations and make validation measurements.
Findings
Two equipment elements; the compressor and the motor, generate the noise produced by the air compressor. eNoise Control was unable to measure them separately.Sound measurements were taken both near-field (within 5′ of the compressors) and far-field (30′ away at the assembly area). eNoise Control compared the compressor noise “finger print” near-field using a 1/3 octave band sound level meter and compared this signature to the far-field readings in the assembly area. We determined that the major noise source was being generated from the motor and radiated noise from the compressor tank. The objectionable compressor noise was determined to be mid-frequency noise at 400-500 Hz range. We presented our findings to our customer.
Recommendations
eNoise Control recommended mitigation efforts at or near the source in order to maximize the attenuation efforts. The primary intent of the recommendations was to decrease the decibel levels without limiting access to the equipment. Recommendations included the following in order of priority:
- Attenuate radiated compressor noise by erecting a sound curtain barrier wall constructed of a 1” fiber glass absorber, bonded to a 1 lb. per sq. inch loaded vinyl noise barrier, suspended from a double track system with floor mounted uprights positioned to form a noise barrier on the two open sides of the corner of the facility where the compressor is located. This suggestion could decrease the compressors radiated noise by 10 – 13 dBA.
- Control reflected noise from the ceiling by adding a roof to the sound curtain wall constructed of modular rigid sound curtain and plywood panels and wrapped with a limp mass barrier valence blocking the openings in the sound curtain wall system created by the track and trolleys the curtain is suspended from.
- Reduce reflected noise by adding acoustical absorption to the adjacent concrete wall and ceiling surfaces using a durable vinyl faced 2” thick sound curtain absorber panels with fiberglass fill, or melamine acoustic foam, on all interior concrete wall surfaces within the curtain enclosure.
- Construct a dedicated room to enclose the two compressors – constructed of concrete block or stud and gypsum board. Implementation of this recommendation should reduce the noise by 20 – 25 dBA.
- Relocate nearby employees to a location further away from the compressors. Moving the noise receivers to a different area of the plant would eliminate the noise problem for these employees immediately.
Results
The manufacturer decided to implement the first two recommendations; to enclose the Compressors with a sound curtain wall on two sides and install a roof over the walls. Validation measurements indicated 13 dBA of attenuation was achieved at 3 ft. outside of the enclosure and a 14 dBA reduction at the location of the nearby assembly workers. Management opted not to build a dedicated room for the compressors because of its permanence if they decided to relocate the compressors at a later date. Also, management did not elect to move the assembly workers because of space limitations and disruption of material flow within the facility. No absorption was applied to the interior walls of the enclosure. The noise complaints from the employees ceased, and management had achieved its noise reduction goals.
Resources
More information about air compressor noise.